Next item on my to-do list was to cut the holes in the instrument panel for my defrost / avionics fans. I briefly put the windshield on the airframe to mark out where it looks like it will sit to ensure I don’t do something dumb. Next I measure where the hole centers should be off the center rivet line to try to make the fans symmetrical. I then drill a pilot hole at the center mark, then follow with a hole-saw in my cordless drill to make the larger hole. Using the fan as a template, I then mark out where the four mounting holes need to be, then drill one of the holes. I cleco the fan in place from underneath and use the fan as a drill guide to final drill the remaining 3 holes.
I plan to dimple the holes and install countersunk screws to keep the glare shield flush. I think I’m going to use the Aerospot Products glareshield, or possibly the one from SFSport Aviation instead of my original thought of using automotive bed-liner paint.
I also decided to change my mind regarding the insulation I am installing on my firewall. Originally I purchased fiberfrax and stainless steel foil and use that as my insulation, but decided to go with lavashield instead. I was thinking the lavashield looked nicer and was easier to install vs the fiberfrax method. Nothing scientific and I’m sure the fiberfrax is superior. I just didn’t like the look of the SS foil over the insulation. Honestly I think the lavashield looks like carbon fiber and at least provides a little insulation value over stock.
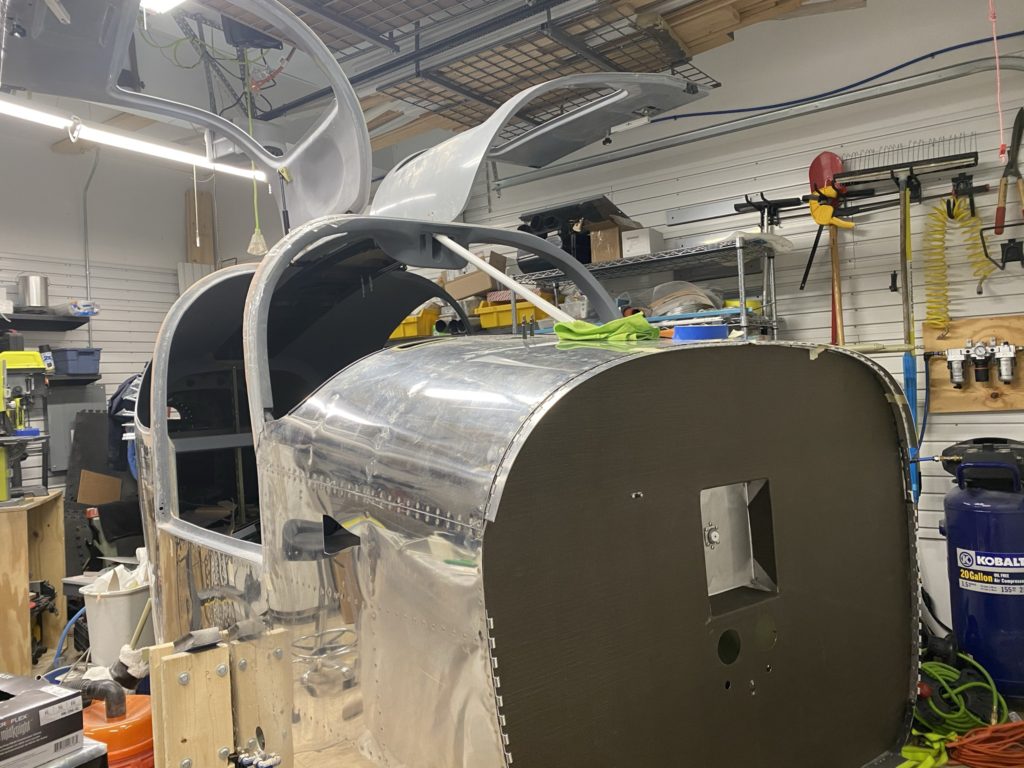
With those items checked off the list, I go back to filler and sanding on the doors and cabin top. I had a very slight gap between the cabin top joggle and the fuse skins that was not due to interference or trimming the cabin top enough, it just didn’t sit completely flush against the skins. I filled this with a little Aeropoxy Light and also decided I was going to cover the blind rivets on the outside of the skin with filler as well to make things look nicer. Again very thankful for the AC/Heat in the garage to make life easier as I sand and blend the cabin top.
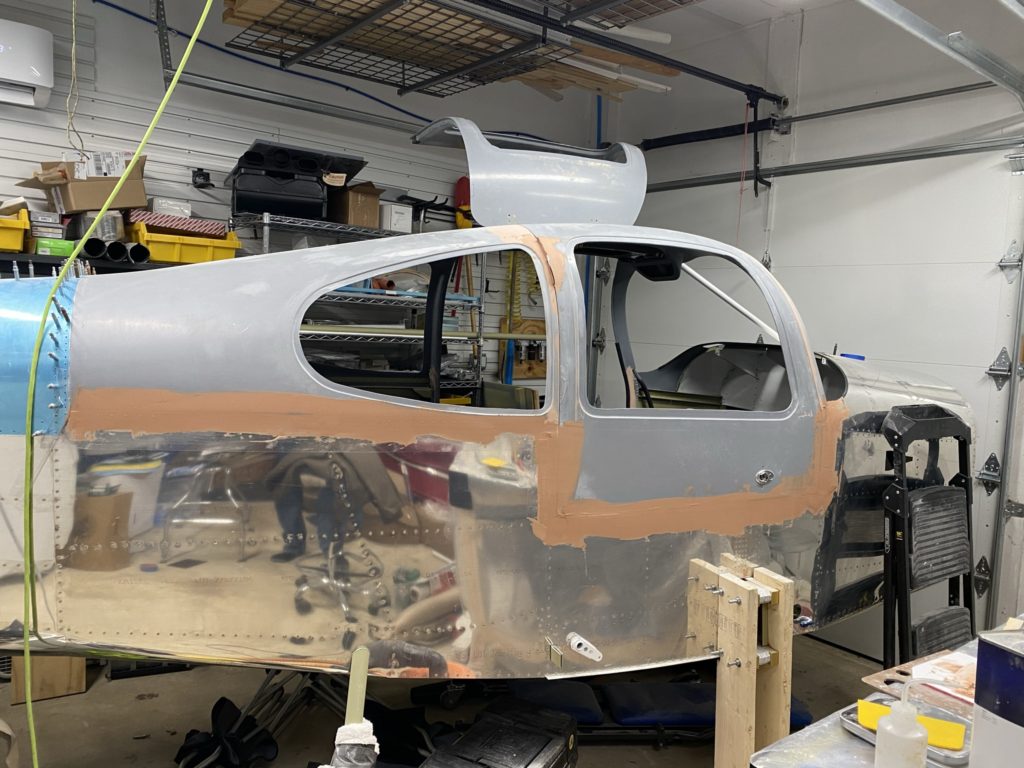